In project 5, “Embedded sensing in 3D printed exo-aid structures”, we aim at developing soft 3D printed parts with integrated sensing structures for the exo-aid systems. These parts will help monitor the electrophysiological processes by integrating pressure sensors, electrodes, wiring and amplifier modules. Some advantages of such parts are:
- Improved ease of use (easy donning and customized fit)
- Intuitive use (sensory-based user-intent determination)
- Higher functionality (by increased sensing possibilities)
- Larger flexibility (sensing structures are flexible as well)
- Improved performance (due to customized sensor designs that tightly conform to the body)
To make these parts possible, we are developing a multi-material fabrication process that combines multiple Fused Deposition Modelling printheads and the deposition of silver inks [9]. We are also developing electronics that enable us to do better measurements with dry, 3D printed, bio-potential electrodes, e.g. electrodes for sEMG.
We also work on fabricating 3D printed force sensors to measure the interaction forces [10,11]. Because the materials used for these sensors often show hysteresis and drift, we work on techniques to linearize the output of these sensors [2,4,5]. Furthermore, because the 3D printed conductors can be non-uniform and anisotropic, we also work on better understanding and measuring the anisotropy introduced by 3D printed conductors [1,3,6,8].
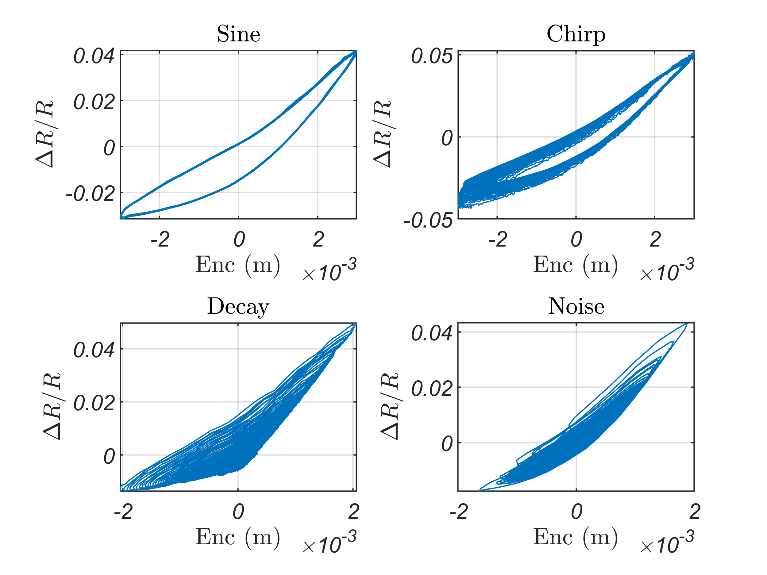
Publication list:
[1] Dijkshoorn, M. Schouten, G. Wolterink, R. Sanders, S. Stramigioli and G. Krijnen, “Characterizing the Electrical Properties of Anisotropic, 3D-Printed Conductive Sheets for Sensor Applications,” in IEEE Sensors Journal, doi: 10.1109/JSEN.2020.3007249 (Open access).
[2] M. Schouten, B. Prakken, R. Sanders and G. Krijnen, “Linearisation of a 3D printed flexible tactile sensor based on piezoresistive sensing,” 2019 IEEE SENSORS, Montreal, QC, Canada, 2019, pp. 1-4, doi: 10.1109/SENSORS43011.2019.8956652 (Open access).
[3] A. Dijkshoorn, M. Schouten, G. Wolterink, R. Sanders and G. Krijnen, “Characterizing the Electrical Properties of Anisotropic, 3D-Printed Conductive Sheets,” 2019 IEEE International Conference on Flexible and Printable Sensors and Systems (FLEPS), Glasgow, United Kingdom, 2019, pp. 1-3, doi: 10.1109/FLEPS.2019.8792279 (Open access).
[4] D. Kosmas, M. Schouten and G. Krijnen, “Hysteresis Compensation of 3D Printed Sensors by a Power Law Model with Reduced Parameters,” 2020 IEEE International Conference on Flexible and Printable Sensors and Systems (FLEPS), 2020, pp. 1-4, doi: 10.1109/FLEPS49123.2020.9239580 (Open access).
[5] M. Schouten, D. Kosmas and G. Krijnen, “Hysteresis Compensation of 3D Printed Sensors Using a Power Law Model for Various Input Signals,” 2020 IEEE SENSORS, 2020, pp. 1-4, doi: 10.1109/SENSORS47125.2020.9278942 (Open access).
[6] A. Dijkshoorn, M. Schouten, G. Wolterink, R. Sanders, S. Stramigioli and G. Krijnen, “Characterizing the Electrical Properties of Anisotropic, 3D-Printed Conductive Sheets for Sensor Applications,” in IEEE Sensors Journal, vol. 20, no. 23, pp. 14218-14227, 1 Dec.1, 2020, doi: 10.1109/JSEN.2020.3007249.
[7] G. Wolterink, A. Umrani, M. Schouten, R. Sanders and G. Krijnen, “3D-Printed Calorimetric Flow Sensor,” 2020 IEEE SENSORS, 2020, pp. 1-4, doi: 10.1109/SENSORS47125.2020.9278640 (Open access).
[8] A. Dijkshoorn, M. Schouten, S. Stramigioli and G. Krijnen, “Modelling of Anisotropic Electrical Conduction in Layered Structures 3D-Printed with Fused Deposition Modelling” Sensors 21, 2021, no. 11, pp. 3710. https://doi.org/10.3390/s21113710
[9] M. Schouten, G. Wolterink, A. Dijkshoorn, D. Kosmas, S. Stramigioli and G. Krijnen, “A Review of Extrusion-Based 3D Printing for the Fabrication of Electro- and Biomechanical Sensors,” in IEEE Sensors Journal, vol. 21, no. 11, pp. 12900-12912, 1 June1, 2021, doi: 10.1109/JSEN.2020.3042436 (Open access).
[10] M. Schouten, P. Patel, R. Sanders and G. Krijnen, “3D Printed Differential Force and Position Sensor Based on Lossy Transmission Lines,” 2021 21st International Conference on Solid-State Sensors, Actuators and Microsystems (Transducers), 2021, pp. 1460-1463, doi: 10.1109/Transducers50396.2021.9495724 (Open access).
[11] M. Schouten, C. Spaan, D. Kosmas, R. Sanders and G. Krijnen, “3D printed capacitive shear and normal force sensor using a highly flexible dielectric,” 2021 IEEE Sensors Applications Symposium (SAS), 2021, pp. 1-6, doi: 10.1109/SAS51076.2021.9530032 (Open access).